1) Cahier des charges
Vous devez réaliser des piédestaux, au nombre de quatre (deux par personne).
2) Conception (136h)
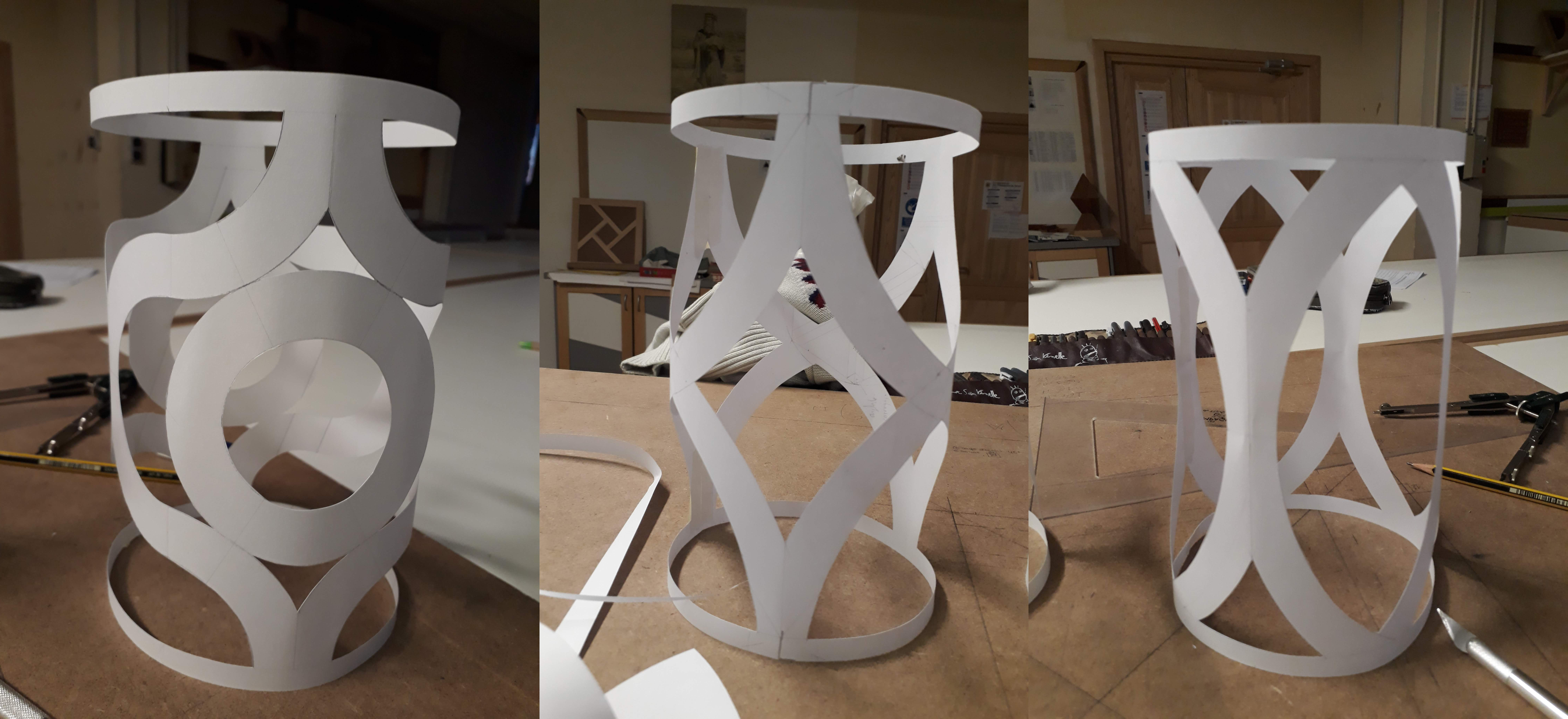
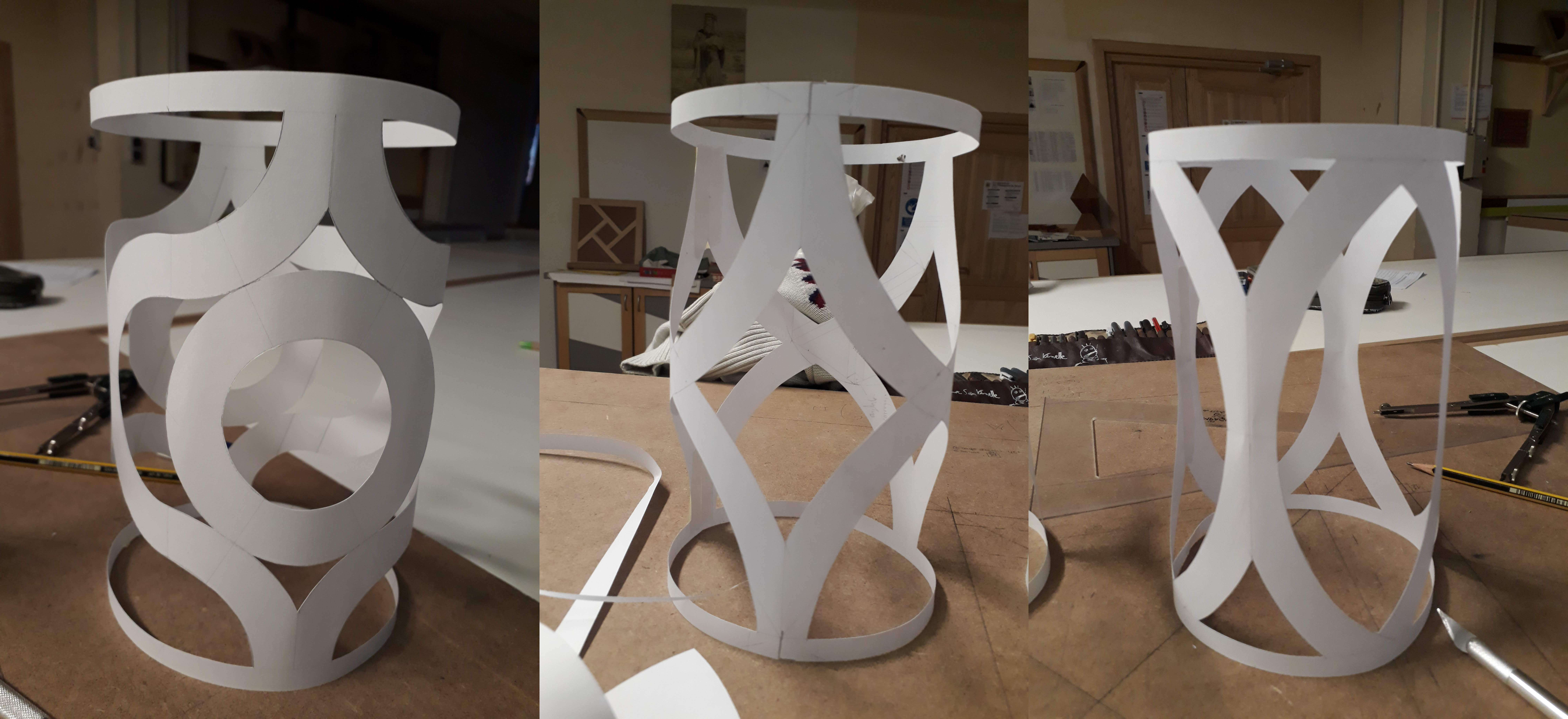
-Recherche d’esthétiques et de proportions. (3h)
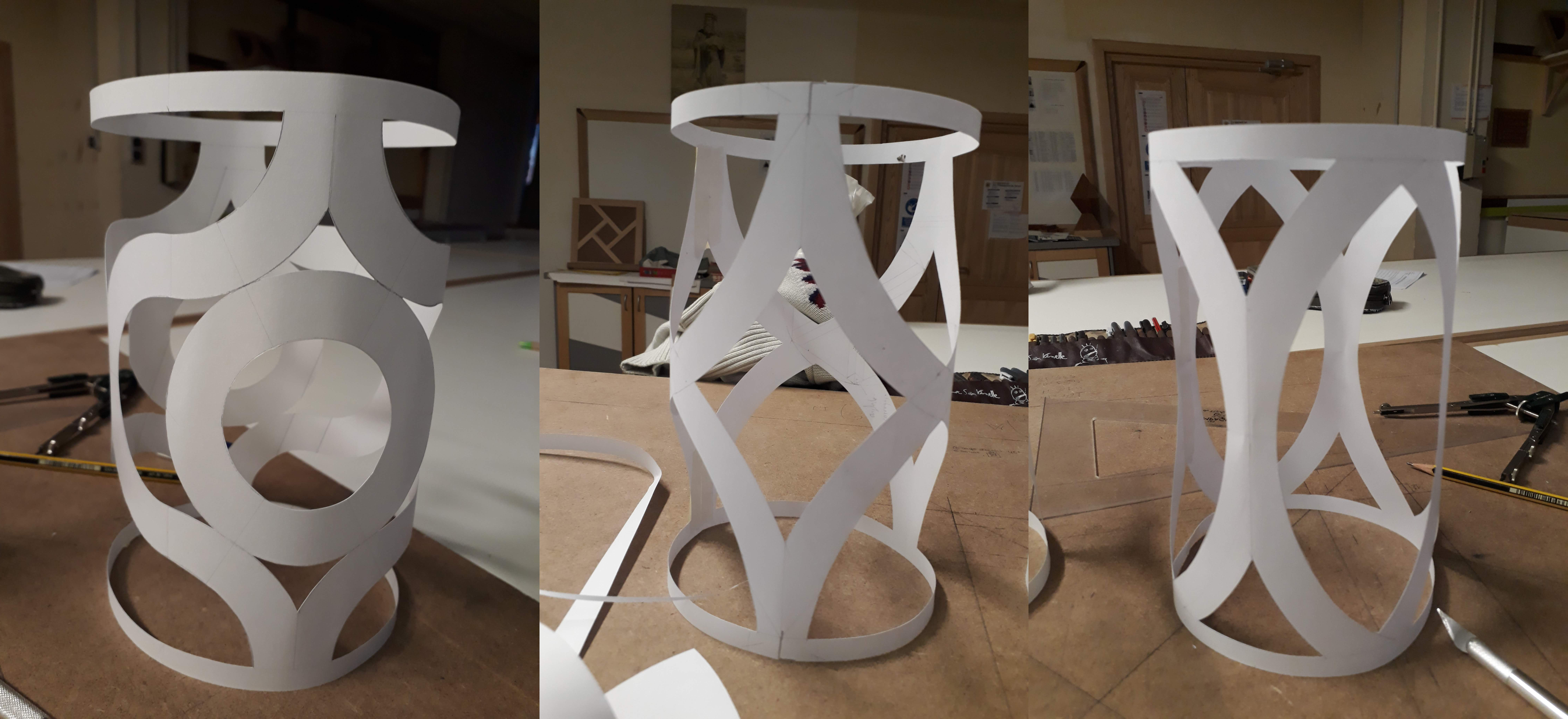
-Réalisation de prototypes (40 heures)
J’ai commencé par un prototype correspondant à un tiers de l’ouvrage. Ce prototype m’a permis de pouvoir estimer un temps pour la fabrication des brins courbes.
J’ai réalisé ce prototype en 8 heures avec une épure tracée sur papier au préalable. J’ai réalisé les chantournements et les débillardés à la scie à ruban en coupant au trait.
Suite à la fabrication de cette ensemble, je me suis rendu compte que le plus long sur la fabrication de ces pièces était le tracé. Je n’avais plus qu’à trouver un moyen pour supprimer cette étape !
Mais ce tiers de cylindre ne permettait pas de se rendre compte du rendu global de l’ouvrage.
J’ai fabriqué des fûts en massif et dessiné les motifs dessus. Pour différencier les essences j’ai utilisé une craie blanche. Les moulures du premier essai étaient trop simple et ne jouaient pas en faveur d’un ressenti agréable.
Quitte à faire des moulures, j’ai repris les proportions et la mouluration d’un piédestal d’ordre corinthien.
J’ai fabriquer les fers pour faire les plateaux de moulure. Ce prototype a été retenu.
Enfin j’ai réalisé deux essais pour représenter les éléments, un premier en gravure laser et un second par transparence.
-Réalisation des plans de fabrication (93h)
Une fois le projet fixé, je me suis lancé à faire les plans sur le logiciel Autocad. J’ai commencé par tracer une élévation et le développement du fût. Puis j’ai défini les assemblages de chaque pièce. A partir de ce point j’ai pu réaliser les tracés de courbe pour obtenir le débit.
3) Fabrication (364h)
-Débit et corroyage (6h)
J’ai effectué le débit à la scie à format à l’aide d’une feuille de pré-débit. Pour celui de chêne j’ai pris la majorité des pièces dans le même plateau de 54mm, afin de conserver une unité de coloris. Pour les brins courbes il me fallait du faux quartier. Le reste à été pris dans les chutes. Pour le débit de cyprès, j’ai choisi le bois afin de faire suivre le fil entre deux panneaux verticaux. J’ai réalisé les feuillets de lamellé collé à la scie à format.
-Les gabarits (68h)
-Gabarit de lamellé collé, moule / contre-moule :
Ce gabarit m’a servi à faire les collages de lamellés en moule contre-moule, et également à couler l’époxy pour solidifier les motifs.
-Boites de chantournement :
Ces boîtes, une avec le rayon intérieur et l’autre avec le rayon extérieur, m’ont servis à chantourner les pièces courbes et à les calibrer à la toupie.
-Gabarit de débillardé des brins et des panneaux :
Ceux-ci m’ont permis d’usiner les chants débillardés d’équerre à la face, à la défonceuse. J’ai fabriqué ces pièces à la main en les traçant.
-Gabarit d'usinage de la rainure :
Ce montage composé d’une table, une butée de profondeur et d’un presseur avec un galet à bille m’a servi à usiner les rainures à la défonceuse.
-Gabarit d'usinage de la languette :
Ce montage, composé une table en champignon et d’un presseur sur ressort, m’a permis d’usiner les languettes par retournement à la défonceuse.
-Les panneaux en lamellé collé (30h)
Après avoir débité les feuillets de lamellé collé, j’ai découpé chaque feuillet à sa dimension finie au cutter.
Ensuite j’ai tracé les éléments de la terre et de l’eau au graveur laser, puis découpé les motifs à la défonceuse avec une mèche de 2mm.
J’ai pu ensuite collé les panneaux dans le moule/contre-moule sans le feuillet de parement.
L’étape suivante était de couler de l’époxy dans le motif pour le remplir, puis enfin de coller le feuillet de parement et d’ajuster l’épaisseur pour régler la luminosité de l’élément.
-Les couronnes de moulures (29h)
Pour réaliser les couronnes de moulures, j’ai coupé les morceaux à la scie à format, puis usiné pour une fausse languette en faisant attention de ne pas déboucher dans la future moulure. J’ai ensuite calibré les couronnes à la défonceuse avec une mèche à galet, en copiant un cercle en médium.
J’ai usiné les moulures à la toupie à arbre fendu avec les fers correspondants, en utilisant un guide continu.
-Les fûts (180h)
L’objectif était de faire toutes les coupes et tous les assemblages sur les masses capables, afin de pouvoir vérifier le pointage sur le cylindre fermé avant de chantourner les pièces.
J’ai commencé par faire les coupes de niveau, puis les coupes d’aplomb. J’ai pointé la mortaise à la bédaneuse et ensuite réalisé le tenon à la scie à format.
La rainure pour le pigeon au croisement des quatre brins a été usinée à la mortaiseuse à mèche. J’ai terminé les assemblages en faisant les barbettes d’ébéniste à la scie japonaise et au ciseau.
J’ai commencé par chantourner les brins suivant les faces intérieures et extérieures du cylindre. Les bois sont placés dans des boites dans lesquelles j’ai effectué le chantournement à la scie à ruban puis calibré à la toupie avec un outil bouffe-tout et galet à bille. Après cette étape, j’ai pu assembler, et le cylindre est apparut.
J’ai également passé les panneaux dans les gabarits de chantournement. J’ai pu usiner les chants des brins et des panneaux avec les gabarits de débillardement avec une mèche de défonceuse à double galet.
Pour usiner les languettes de 5mm sur les panneaux en cyprès, j’ai commencé par mettre un coup de trusquin à 4mm pour faire office de par-éclat et usiné une languette de 3mm par retournement sur un champignon.
Pour terminer les arasements des panneaux j’ai assemblé les cadres (2 brins + 1 traverse) et relevé les développements des faces avec du papier que j’ai ensuite collé sur les panneaux. J’ai fini les arasements des panneaux avec un rifloir en ajustant petit à petit.
Une fois tout les éléments du fût terminés, j’ai pu procéder au collage. J’ai collé les fût par moitié puis les deux moitiés ensemble.
J’ai poncé le tout avec du papier de verre 120p puis vernis avec du vitrificateur à parquet. J’ai assemblé les couronnes de moulures avec des tourillons collés.
-L'électricité (20h)
Pour la partie électricité, j’ai opté pour des bandeaux LED, car ils peuvent fonctionner avec des piles et sont peu énergivores. Pour avoir un système électrique entièrement démontable j’ai pensé une quincaillerie que j’ai imprimé en 3D. Je l’ai dessinée en 3D sur Autocad et exporté un fichier STL compatible avec l’impression 3D.
Une fois toutes les quincailleries imprimées (environ 25 heures d’impression), je les ai fixées dans les fûts.
J’ai procédé à la fabrication du circuit électrique, les piles sont branchées en série pour obtenir une puissance de 12V (8 piles AA) et les LED sont branchées en parallèle. Tout le circuit est soudé à l’étain et les soudures sont protégées avec des gaines thermorétractables.
Pour finir, j’ai usiner des compartiments pour ranger les boîtiers de piles, et inséré le circuit dans les fûts.
-Les arasés du dessus (31h)
Pour fabriquer les médaillons et les panneaux en cyprès rayonnant, j’ai réaliser des gabarits de calibrage en contre-plaqué en imprimant les tracés. Les calibrages ont été fait à la défonceuse avec une mèche à galet. Les rainures ont été faites à la toupie avec un outil à rainurer. Les languettes sur les cintres ont été faites à la mortaiseuse à mèche par retournement sur une contre forme des cintres comme guide. Les languettes sur le chant droit ont été faites à la toupie.
Les pièces de la ceinture extérieure sont assemblées par queue d'aronde glissière rayonnante, pour les fabriquer j’ai calibré les pièces à la toupie et passé les rainures avant de faire les assemblages. Pour tailler les queues d’aronde, j’ai fabriqué des boites à coupe et taillé les assemblages à la scie japonaise. Pour la pièce à queues parallèles, j’ai tracé les pièces à l’épure et taillé à la scie japonaise.
Les moulures de la corniche seront passés après assemblage complet afin d’éviter les éclats sur les assemblages.
José Das Neves